In 2020, the Alberta provincial government of Canada launched the Carbon Fibre Grand Challenge (CFGC). Alberta is one of two provinces in my country that has oil sand deposits that have been mined for decades to create synthetic crude. As the world starts phasing down the burning of coal, oil and natural gas because of their greenhouse gas contribution associated with atmospheric warming, the industry by the end of this decade will be in a state of rapid transition. In a world where we will limit the burning of fossil fuels including synthetic ones, will there be a place for Alberta’s producers? Can the asphaltene, bitumen and synthetic crude rather than being burned, serve other purposes?
The Carbon Fibre Grand Challenge could be that other purpose. Businesses, universities, not-for-profits, and government laboratories were invited to take the challenge. Thirteen entries reached Phase 3 this year and now five remain to battle for the prize of $15 million Canadian (approximately $11.2 million US).
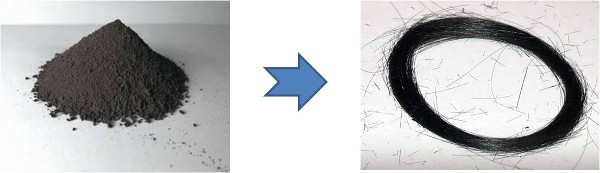
The five have to produce from oil sands raw and semi-processed products, from 0.5 to 1 kilogram of carbon fibre daily (see picture above). They then have to show they can scale their method to yield 5,000 tons annually by no later than early in the 2030s. And finally, they must produce the carbon fibre at a cost 50% below what it sells for now which is somewhere between $20 and 33 US per kilogram (approximately $9.10 to $15 per pound).
What makes carbon fibre an attractive alternative to the making and selling of synthetic crude? What is the current and future demand for it? According to Fortune Business Insights, carbon fibre is the product of choice for aerospace, automotive, construction, defence, medical, renewable wind energy, and sports equipment industries. Revenue in 2023 will end up around $3.31 billion and will grow to a forecasted $5.96 billion by 2030.
Carbon fibre has a low-weight-to-strength ratio. It is five times stronger and twice as stiff as steel. Better yet, it doesn’t rust and is chemical resistant. In the drive to make automobiles lighter and more energy efficient, carbon fibre parts are being used extensively by automotive manufacturers.
Today, carbon fibre’s largest producers can be found in the United States, Japan, South Korea, Germany and Belgium. Their manufacturing processes are labour-intensive. Canada has little in the way of manufacturers, so kickstarting production in Alberta would make the country competitive with the frontrunners.
For CFGC, a team of experts selected the best projects that now have 36 months to prove themselves. So who are the companies still in the competition?
Carbomat Inc. is Calgary-based and a 2022 spinoff from the University of Calgary. They claim they can drive down the cost of producing carbon fibre by 60% using asphaltenes and other waste materials from oil sands mining while reducing emitted greenhouse gasses in production by 50%.
Enlighten Innovations Inc. is a novel energy company with offices in Calgary and Denver, Colorado. It has a patented sodium ion-selective ceramic membrane technology that enables low temperature, high conductivity and selectivity of sodium ions. it intends to produce carbon fibre using its technology to desulfurize asphaltenes.
NORAM Engineering & Constructors Ltd. was founded in 1988. Vancouver, British Columbia-based, the company builds custom solutions for resource industries. Its entry into the CFGC is to provide a low-temperature stabilization and bulk processing technology for the production of low-cost-asphaltene-based short carbon fibres.
Thread Innovations is an Edmonton, Alberta-based company that aims to disrupt the production, economics and adoption of carbon fibre. It uses bitumen vacuum refinery residue-derived and asphaltene-based precursors to manufacture carbon fibre at a higher scale and far lower cost than its competitors.
University of British Columbia’s Department of Applied Sciences is a CFGC finalist having developed a unique process for spinning finer fibres while maintaining their structural integrity. Two distinct products, regular micro-diameter and nano-fibres are both being produced using bitumen. The process can yield fibres costing less than $12 per kilogram (approximately $5.45 per pound).
Alberta’s bitumen and asphaltene are described by Bryan Helfenbaum, Associate Vice President for Clean Energy, at Alberta Innovates, as ideal feedstocks for making carbon fibre. For the province, it represents an opportunity to diversify its economy while reducing carbon emissions. And it means that demand for Alberta bitumen can now be directed to the fast-growing market for carbon fibre.