April 24, 2017 – Duke University researchers have published the results of recent work they have done with low-cost 3D printers to create hydrogels that can act like cartilage for knee repairs. The printable hydrogel can be engineered to replace a worn joint matching the shape and mechanical properties of a healthy knee.
The focus of the Duke research was on creating a meniscus, the cartilage that cushions the inside of the knee between femur and tibia. The meniscus acts as a natural shock absorber and is the usual suspect when a knee begins to fail. I know this from personal experience since my mid-20s because I have severe osteoarthritis in my left knee and less than 10% of my original cartilage. I have had MRIs, x-rays and ultrasounds to check the health of my knee on several occasions. A number of years ago I was informed that knee replacement was recommended. But I have been reluctant to consider a mechanical knee joint believing that I would be better off holding onto my original parts as long as possible. That’s made me look at other therapies including cortisone, hyaluronic acid, platelet and stem cell injections. Currently, I get cortisone injections every three months.
But the work at Duke is fascinating even if it is still at an early stage. Duke used a two-step process to 3D print, at room temperature, a series of hydrogel implants to create a synthetic meniscus precisely designed to fit a knee joint. The choice of material, hydrogel, was based on its inherent adaptability, biocompatibility, and  stability when placed within the body.
Finding the right hydrogel was the important breakthrough. It needed to match the properties of cartilage. At the same time, it had to be printable. Creating accurate digital renderings that could be translated to a printer was the least of the challenges the inventors faced. MRI, x-ray and other imaging technologies could accurately produce 3D representations which could then be rendered to a 3D plot with instructions sent to a printer.
The search for the right hydrogel led to the discovery by a young Duke graduate student, Feichen Yang, who combined two hydrogels together and then added liquid clay to produce a combination of stiffness, softness and stretch. Yang combined the three weaving the distinct polymer chains and clay particles together which formed a liquid. One of the tricks was to alter the proportions of the hydrogel constituents depending on the location within the meniscus. The clay served two purposes. It helped create a liquid consistency that allowed the hydrogel to flow through the print head. Once through the clay hardened giving the hydrogel a stable structure. One meniscus took a day to print.
What Yang has invented can apply to more than knee joints. In fact, it is probably the start of what will be a new printing industry, creating replacement parts for people with damaged hips, knees, shoulders and other areas of anatomy. The variable will be in the materials extruded through the printing head. Even living cells may serve as printer ink.
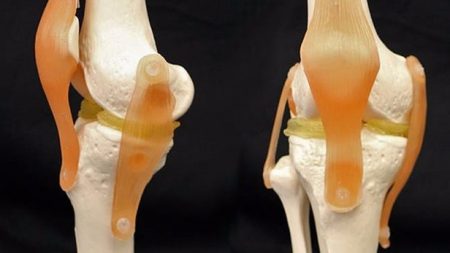
[…] Photo credit: Feichen Yang, Duke University https://www.21stcentech.com/3d-printing-save-arthritic-knees/ […]