April 11, 2020 – A multi-authored, multi-institution, and multi-business report describes the technologies and policies needed to decarbonize our global industry by 2070, keeping global atmospheric warming to no more than a 2 Celsius (3.6 Fahrenheit) rise. Appearing in the journal, Applied Energy, it identifies measures that collectively can lead to net-zero industrial emissions within the timeframe.
The report looks at both the supply and demand side of world business. It introduces technologies and policies that include energy efficiency, carbon capture, electrification, and zero-carbon hydrogen feedstock for multiple industrial, residential, commercial, and transportation purposes.
The focus is on eliminating the 33% of GHG emissions contributed by three key industries (see graph below) that are among the main contributors to global warming. They are the cement, iron and steel, and chemicals and plastics industries. Alternative net-zero carbon methods to produce these critical materials exist. Acceptance to move to these methods for these primary industries has been the challenge.
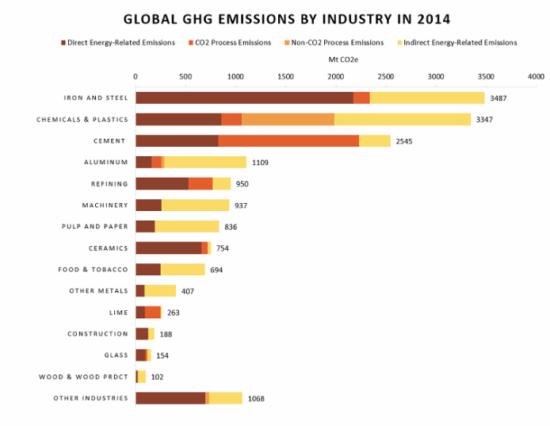
Many on this planet are concerned about material waste. It is pointed out to us that our oceans are filled with single-use plastic, that our landfills are home to materials that can be repurposed. We are becoming more aware of the need to create circular economies within industries through better design, reusability, refurbishment, and recycling.
So how do you get industry to make the move to net-zero and adopt a circular economy business model?
- Through policy changes directed by national governments,
- Through the education of the public to reject products and services from companies that ignore the need to achieve net-zero emissions.
A well-designed policy is an innovation accelerator.
So what policies can do this?
- Putting a price on carbon is seen as an effective way to move industries to adopt net-zero manufacturing and distribution technologies.
- Mandating data collection to accurately measure carbon emissions in these industries to set timetables, milestones, and targets for reduction.
- Implementing financial support to foster research and development within these primary industries for net-zero technology deployment.
- Using government purchasing power through net-zero procurement and design, and reusability, refurbishment, and recycling requirements in every request for proposal, and request for quote.
- Accompanying the replacement of existing industrial processes with programs to provide a just transition for workers and communities impacted by these changes.
Why pick on these industries to tackle global warming?
Industries are looking constantly for productivity and process improvements to gain competitive advantage. But now the focus of that improvement can include low-carbon and zero-emission technologies which can become competitive advantages as well, and potential revenue-generating products to be offered to the global market. And we already have many of the breakthrough technologies at hand, from 3D-printing to new materials, chemical catalysts, and innovative automation processes that can contribute to GHG emission reductions.
An Interesting Proposition: Global Hydrogen Adoption
Renewable-electricity-sourced hydrogen created through electrolysis is seen as critical to industries transitioning to net-zero emissions. Hydrogen that is not produced from fossil fuels is seen as key to decarbonizing transportation, heating, and industrial production. But hydrogen requires the rapid scaling of its production and the building of a hydrogen distribution and storage infrastructure equivalent to what oil and gas have today.
A Carbon Rethink is Needed in All Three Manufacturing Sectors
Cement – production exceeded 4 billion tons in 2018 with carbon dioxide (CO2) release occurring both at the beginning of the process in terms of energy input as well as during the manufacturing process. Cement’s contribution to GHGs globally is 8-9%. Changing the energy used for production from thermal coal and natural gas to renewable can remove input emissions. But in manufacturing, it becomes necessary to reformulate the chemistry of cement production to create significant CO2 reductions. There are solutions out there that bind CO2 into cement turning it into a carbon sink through capture during production. And then there are manufacturers who produce cement using captured carbon from third parties. A Halifax-based cement manufacturer has proven the efficacy of the latter in developing green cement products.
Global steel – production amounted to 1.8 billion metric tons in 2018 with 71% produced using blast furnaces, and the balance largely using electric arc furnaces. A blast furnace produces from 1.8 to 2.8 tons of CO2 per ton of steel. Arc furnaces if using a decarbonized electrical power source produce as little as 0.7 tons of CO2 per ton of steel. Most of these producers are operating at the limit of what is practical in terms of efficiency which means to reduce CO2 emissions will require one of two things: implementing CCS in production processes, or creating a new process that uses hydrogen.
Chemicals and plastics – produce nitrous oxide and CO2, both potent greenhouse gases. These end products largely come from fossil fuels. One way to significantly reduce the GHGs coming from this sector is to source the feedstock not from fossil fuels but from elsewhere.
Substituting biomass for fossil fuels may be the answer. Biomass contains lignocellulose, the dry remains of plant materials and the byproduct of saw and paper mills, is the most abundant source of organics materials on Earth. Creating commercial technology capable of turning lignocellulose into chemicals and plastics represents one way of dramatically reducing this sector’s CO2 contributions.
Used plastics represent another feedstock for chemicals and new plastic. The challenge for this to become commercially viable lies in ensuring a steady source of usable feedstock materials. Poor implementation of recycling programs, and contaminants in the waste plastic, have made this material source problematic.
CO2 itself can be used as a feedstock to produce chemicals. This is where carbon capture combined with hydrogen can become a significant contributor to the chemical and plastic industry. But using CO2 as a material source to become commercially viable requires a significant increase in energy produced from renewable sources exclusively.
Separation technologies can also be used to produce chemicals. These processes use thermal distillation, drying, and evaporation. The energy input represents the largest source of GHG emissions. But switching to renewable energy input can make separation technology more efficient. And where will this have the greatest impact? In desalination plants where increased water scarcity from climate change is an impetus to improve separation processes.
Circular Economy Principles Need to be Adopted
What gets produced in all three industrial sectors must keep in mind that less new is better for the environment. That means extending the life of the products that get produced whether raw steel and concrete, cars, trains, or buildings. Today, a typical building in the Developed World has a life of between 60 and 80 years. Most buildings can last far longer than that but the cost-effectiveness of keeping them decreases over time for a number of reasons including rising land value, and the cost of upkeep. Increasing the longevity of buildings and making them easier to maintain and more flexible for repurposing and expansion is therefore, an important way to reduce GHGs. The same can be said for cars and trains. And buildings don’t have to be made largely of steel and cement. Today wood is emerging as a sustainable material substitute and serves as a permanent carbon sink.
3D-printing fits well within the discussion of the circular economy. Also known as additive manufacturing, it changes the entire process involved in making things whether buildings or cars. It eliminates metal casting, milling, drilling, and grinding. It is flexible in terms of the raw materials needed and the amounts used. There is little to no waste and what is produced as a byproduct can be reused as feedstock for a future project.
What Are the Milestone Predictions for Achieving Net-Zero?
The roadmap for policy and implementation to achieve net-zero emissions will likely occur in waves following these approximate timelines:
- Demand-side interventions and existing commercialized efficiency technologies will dominate until 2035.
- Structural shifts in all three industrial sectors will become more visible between 2031 and 2050.
- Hydrogen and other net-zero technologies and processes will follow to dominate by 2070.
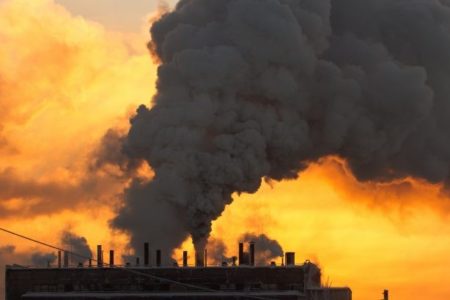